Closed system for wild alpine trout
- 20. januar 2020
To ensure the recruitment of juveniles to watercourses damaged by hydropower, Hallingfisk has built a new hatchery and juvenile production unit. Closed water circulation systems based on reuse of water, protects the fish from diseases and provide stable water quality. A tailor-made monitoring system keeps control of the system.
In the autumn wild couples of mature fish ready to spawn are caught with traps. The fish are stripped from eggs and sperm, mixed and brought to the hatchery. Obtaining the right genetic material is an icy job, but there is no way around : The fish to be released must come from the right stock and the very same water course.
Thousands of red eggs are now lying on the shelves in the hatchery. The few ones that are not viable are carefully removed with tweezers. After hatching in January, they start to live on the yolk sac, until they meet the first challenge – the first feeding.
– The eggs looks nice and have the right colour, so this looks promising, says Sigrunn Røthe Mørk. For many years she has worked with securing juvenile fish for the cultivation of regulated mountain lakes. She often travels with a fishing rod in the mountains herself.
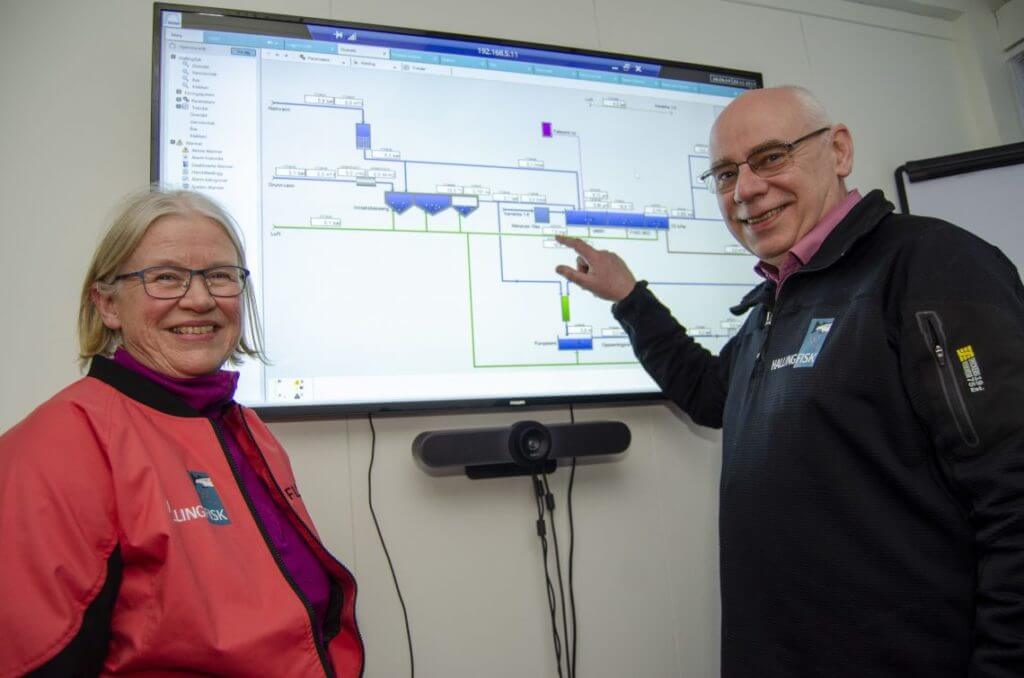
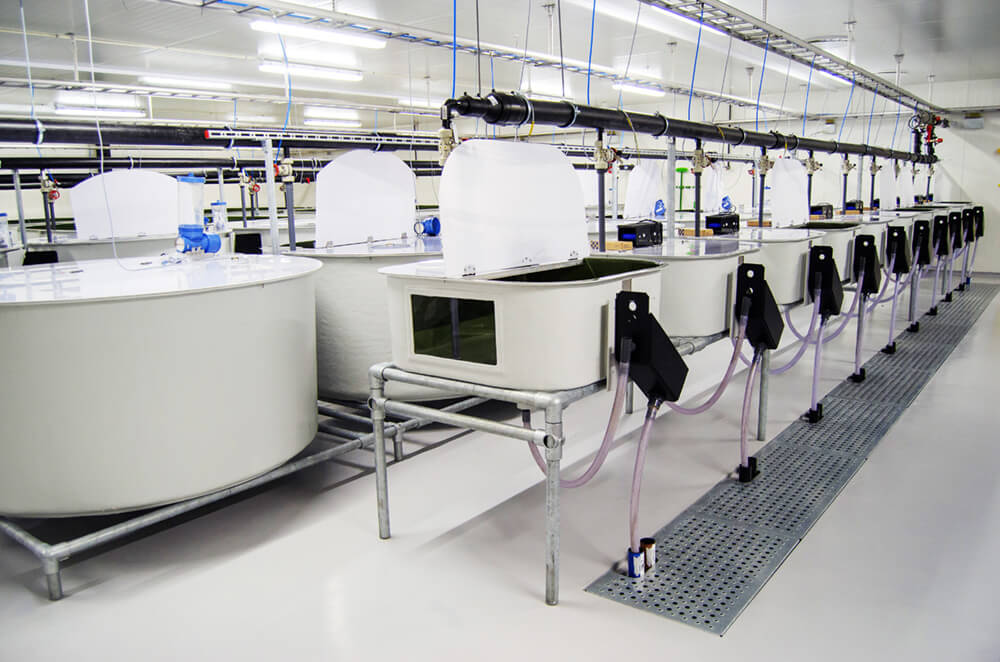
Mountain lakes
Since old times, mountain trout have been part of the local harvest in Hallingdal. The elder of the villages can with a glance at the fish tell which lake it comes from. When the mountain lakes were regulated into hydropower almost seventy years ago, mitigating measures became necessary, and today the landowners receive money from the energy company E-Co to re-stock with juvenile fish. A dozen mountain lakes between Hallingskarvet and Reineskarvet, also called Skarveheimen, are all supplied with juveniles. Some other lakes ar also included in the scheme, several are connected via tunnels.
– This area was one of the first to be regulated in this country, the release of fish is compensation for the damage hydropower has caused to the watercourses. The hatchery provides viable stocks and secures good fishing for locals and tourists, says Torbjørn Aalton, who together with Røthe Mørk has the operational responsibility for the new hatchery.
The goal is to produce 120,000 first-class yearlings, from four separate fish stocks, for release in the respective areas. In addition, some fish are stocked into private waters with limited spawning opportunities, here there are strict rules for using local fish stocks.
– For thousands of years, mountain trout have adapted to their watercourse, we must take care of this diversity, Aalton emphasizes.
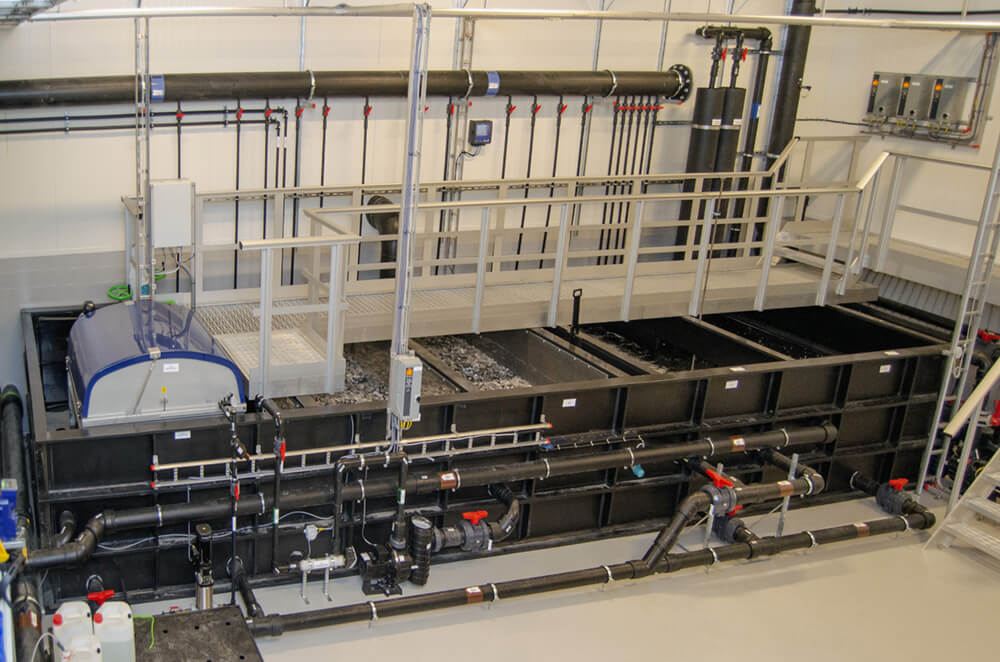
Hydropower
In the past, juvenile fish were farmed in connection with the Hol power plant in Hovet, but challenges with the operation meant that it was decided to build a modern, closed facility. The new facility is located at Kleivi Industrial Park in Ål in Hallingdal. The aquaculture facility itself with water treatment was built by Sterner and has cost approximately NOK 20 million. Everything is located in a former industrial area, in a closed system no fish can escape from. The facility is probably the world’s most advanced for wild fish, and based on reuse of water, it is probably also the safest.
In the previous plant at Hol, untreated water from the watercourse was used, the disadvantage was that it was affected by the cooling function in the power plant, so the temperature could fluctuate abruptly, which was not good for the fish. There were also challenges with a parasite called costia, which in turn could lead to fungal infections.
– Now that we have a closed facility, we can offer stable conditions and the fish are protected against most negative factors. In the building, there are security locks and barriers where we have control over what enters the facility, we talk about full control, says Aalton.
In the same way, the facility is closed from the outside world and is thus also 100 percent escape safe.
– Even though we use local populations, there are requirements for this from the authorities, we reckon that there are good reasons for this, says Aalton.
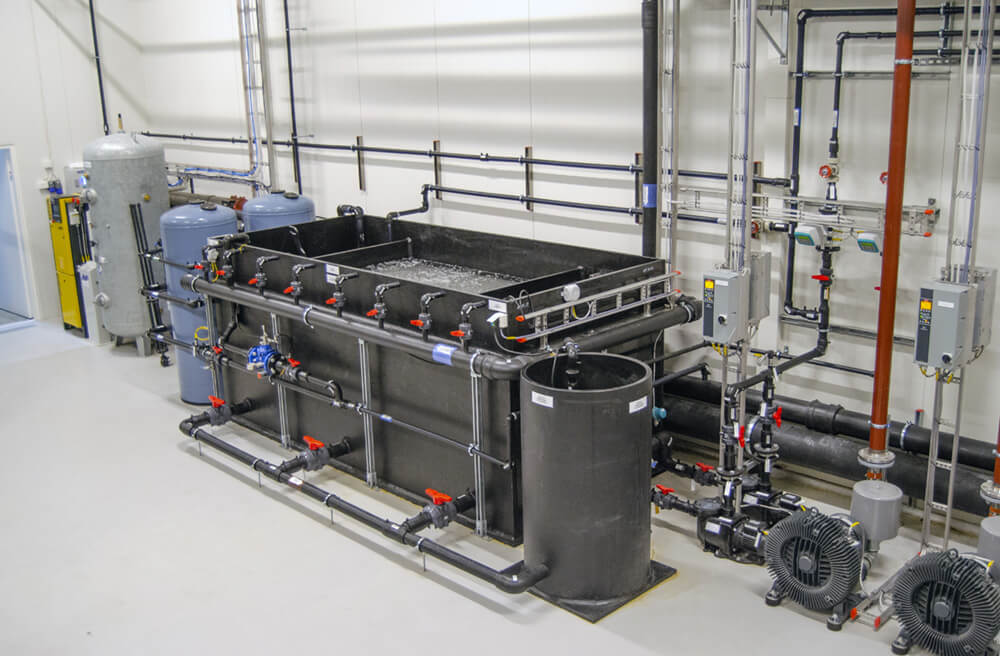
Well
The raw water is obtained from a sixteen meter deep groundwater well just outside the wall of the fish plant. The facility is located on a peninsula in Strandafjorden, and the water is of good quality. The groundwater is disinfected with UV, particle filtered and aerated.
– We were a little worried about the quality since this is an industrial field. The analyses show stable quality, it is naturally filtered in gravel masses, for safety’s sake fully treated, Aalton explains.
Fertilised eggs that arrive at the plant is disinfected and moved in through a hatch in the wall. The fact that the plant is isolated from the outside world and based on water recycling means that the fish are well protected.
– In order for the eggs to have a natural development, groundwater is used, extracted outside the recycling plant itself. However, we have seen that the groundwater is warmer than we are used to, and it has therefore been necessary to cool the water, in this way can maintain a more even temperature and ensure that it does not exceed 8 degrees, which is harmful to the eggs , explains Aalton.
While the hatchery receives newly treated groundwater, the water in the fish tanks goes into circulation, except for about 1-2 percent replenishment, to replace water that is lost during the water treatment. Any excess water is taken out after the water has been cleaned and goes out into the fjord.
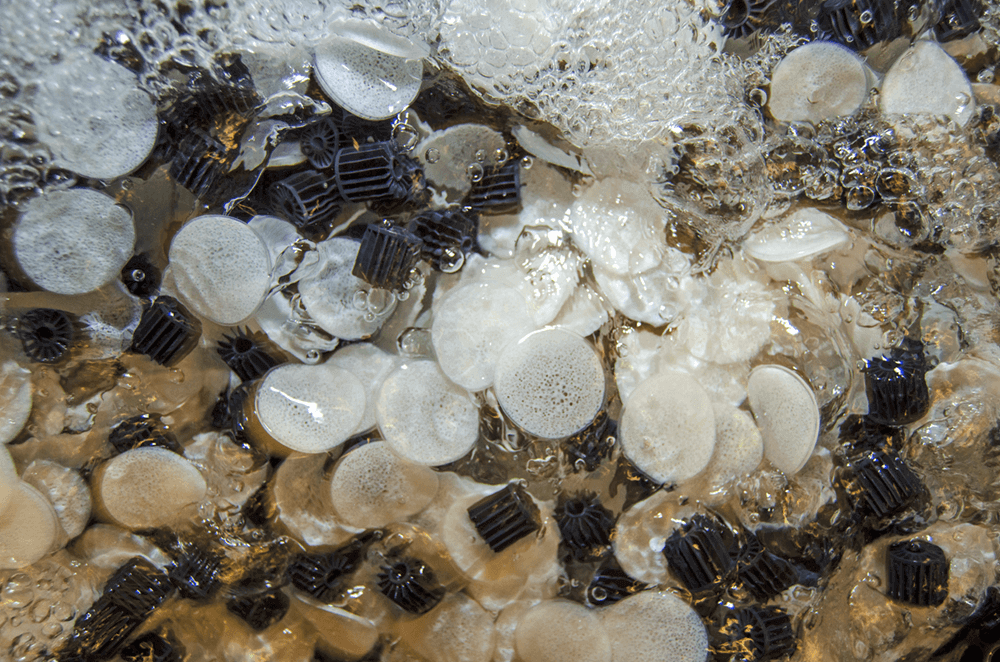
Filter
After the water passes through the fish tanks, it passes through a mechanical filter, biofilter, fixbed particle filter and CO2 aerator. In addition, pH adjusting agents are added. To keep water consumption low, pure oxygen is added directly to the tanks. The oxygen is extracted from air on site, stored in tanks and also acts as an emergency backup. Should the power fail, there is a spare pressure tank with oxygen, which can deliver for a while without power. In the event of a possible longer power failure, municipal mains water is
used, which then goes into a carbon filter, particle filter and aeration.
– The old plant used cooling water from the turbines. Nature provided the conditions, for better or worse. Now we are the ones who control the water quality one hundred percent, and that is a big responsibility. The plant in fats contains both a wastewater treatment plant and a waterworks, there is a lot to get acquainted with, says Aalton.
After the water has been a round through the plant, new water is added as needed. A pump lifts the water seven meters up so that it can flow back through the system. Another pump drives the CO2 aerator, while the third is on standby. The piping system constitutes the buffer volume in the plant, which is dimensioned for the supply of 56 kilos of feed per day.
– Because there is only one pump that drives it all, it is easy to manage. After the water is purified in the various steps the water is ready for a new round, the amount of purification sludge is no more than that it can be sent to the municipal sewer. The facility is thus sustainable and does not harm the environment in any way, says Aalton.
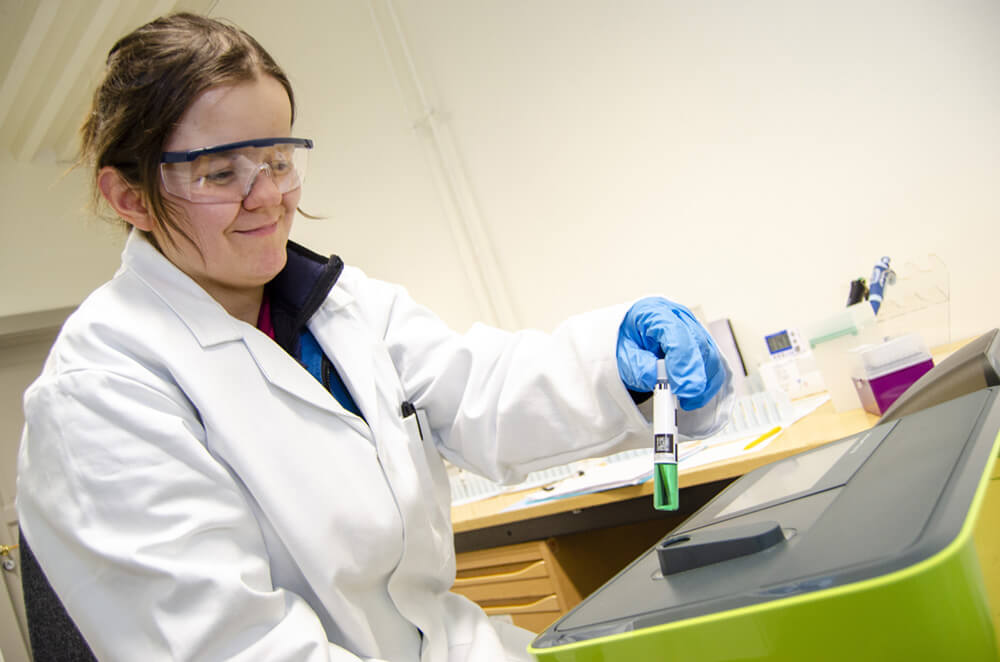
Waste
Even if there are no fish in the tanks yet, water has recently begun to circulate and nourish the bacteria, so that the biofilters are activated for initial feeding.
– The biofilters are at a minimum load when the little ones start to excrete waste products is an advantage. We have warmed up a bit on the water to speed up the process, Sigrun explains.
To ensure good operation, all components in the system are controlled from a control and logger system on a PC. Here pumps, aerators, water levels, oxygen values, temperature, pH, water flow, etc. can be seen on the screen. If a measurement deviates, there is a warning, and measures can be taken immediately. A number of functions are also started automatically in the event of deviations, for example extra oxygen is dosed if the values should drop behind certain levels. In addition, the system will run itself up after a possible power failure. All components have memory, and everything will start in the position it was in when it stopped. So no extraordinary procedure is necessary. Operating system and external notification are equipped with battery backup, as are network connection and control PC. The control system is tailored by Sterner and is based on an open interface (Scada). The solution is affordable and expandable, and all PC-moduled modern equipment can be integrated to the plant and into the operation.
– We can also control the facility from digital surfaces at home, we log in via a VPN tunnel, it’s like logging in to online banking. The same applies to alarms in the event of deviations, we can control this with a smart phone. This gives us both a great opportunity to get to know the facility, and follow up via on-call arrangements, we look forward to releasing the first fish next autumn, we will see how fast it grows, says Sigrunn Røthe Mørk.
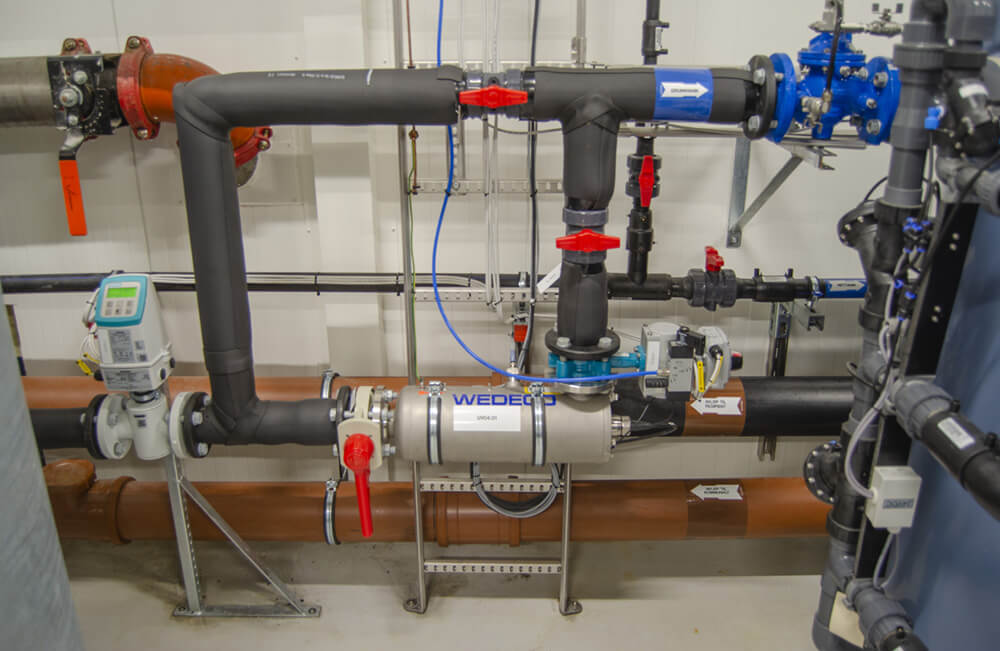