Profitable RAS combined with sea cage farming
- 9. desember 2019
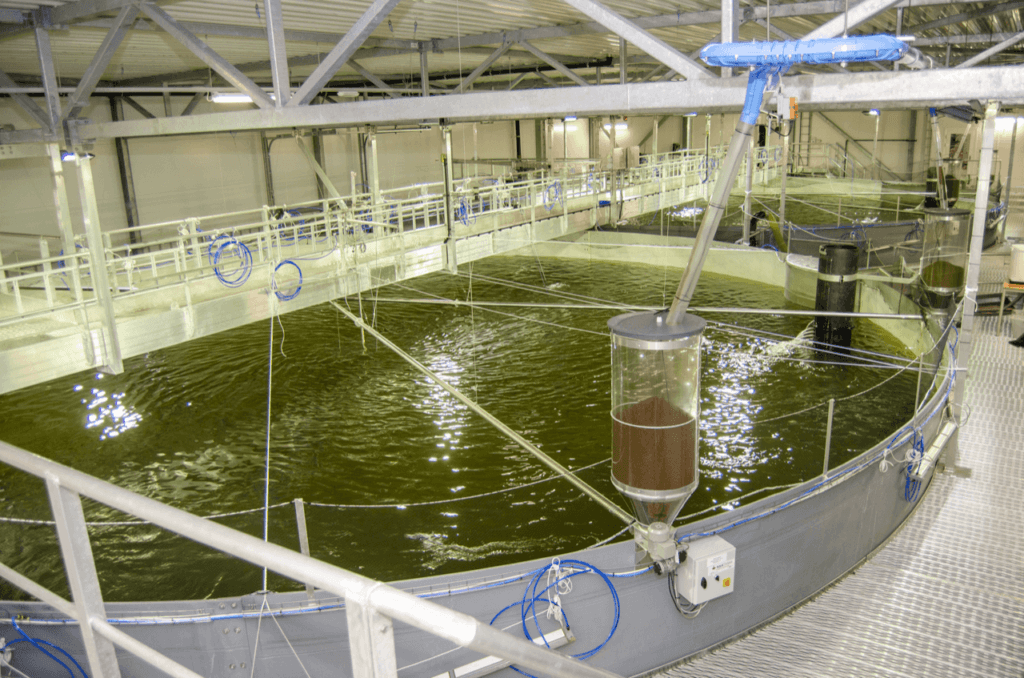
After six months of operating the RAS plant, company Eidesvik Settefisk has achieved good growth, reduced feed consumption and being able to save great amounts of water.
The Eidesvik group based in Bømlo has one concession for juvenile fish, three concessions for cage production and exports a total of 4,000 tonnes of salmon per year. For a little over half a year, the company has operated its new RAS facility, and recently launched the second group of large smolts into the sea cages.
They used to operate the smolt plant with full flow-through with fresh water was pumped from a nearby water source. The starting point for investing in the new RAS facility was limited on access to fresh water, and also the benefit that in RAS the smolts will be larger and reduce production time at the sea.
– We have a good water source but a small catchment area, which creates limitations if there is little rainfall. With RAS, we have significantly reduced our need for water. The RAS plant only needs 0.75 per cent new water for each loop in the system. We achieve better security for our water sources, a good environment for the fish and more predictable production, since the temperature is higher and growth can be controlled, explains Mathias Eidesvik at Eidesvik Settefisk.
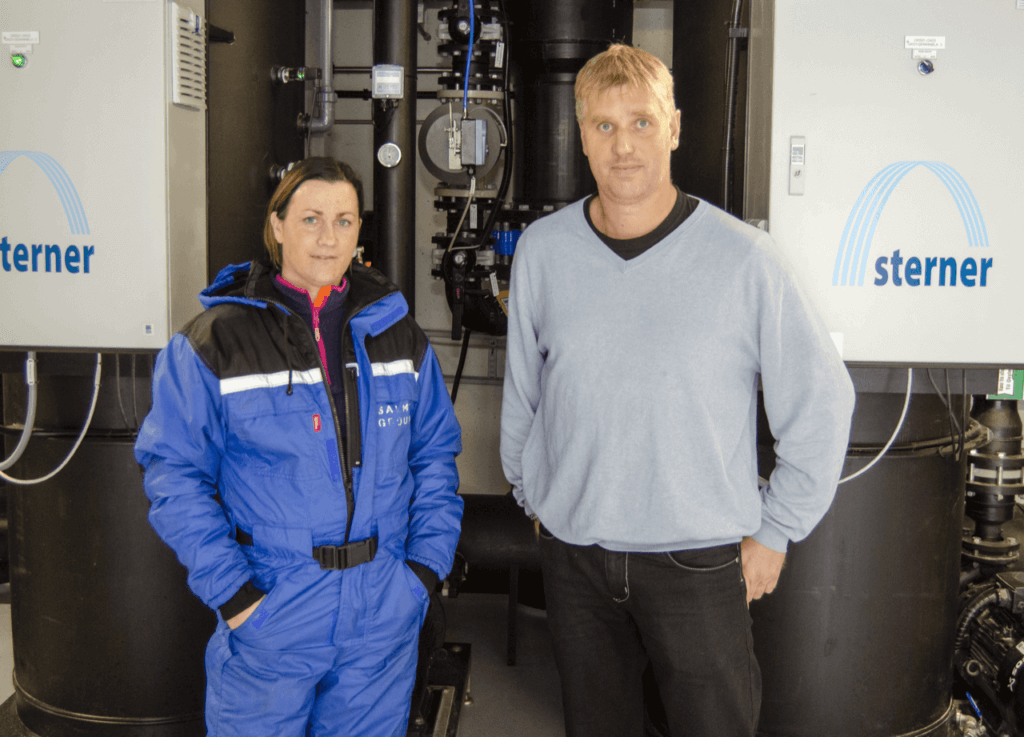
The company still wants to use flow-through for the hatchery, start feeding and fry units, being cautious to fulfil biological needs during the first weeks of the life of the fish.
– We keep “virgin water” for hatchery and starter feeding, the quantities we are talking about are also small and the growth is good, and we can control the temperature of the fresh water we collect according to the depth of intake in our reservoir, says Eidesvik.
More biomass
From now on the plan is to grow the smolt up to 500 grams in the RAS. As the time of smoltification can be controlled with light, maximum biomass can be achieved. This has great economic significance for the operation of the sea cage farm. The concession limit is for a maximum quantity of standing biomass in the sea cages. Keeping high biomass in the sea at all times means that the growth per day is much larger than with a fluctuating biomass.
– We are also subject to restrictions as to when in the season we can launch fish in the sea cages. Now we can start with more biomass and maintain a higher yield in the sea. Since the smolt is larger, we expect to reduce the production time in the sea cages considerably, and so make better use of the sea cage facility, says Eidesvik.
However, RAS facilities are a new experience and require expertise in water treatment and process. Gaining experience with the plant’s functions and operating properly has a high priority.
– So far we have run the pumps for half a machine, but it looks promising, he says.
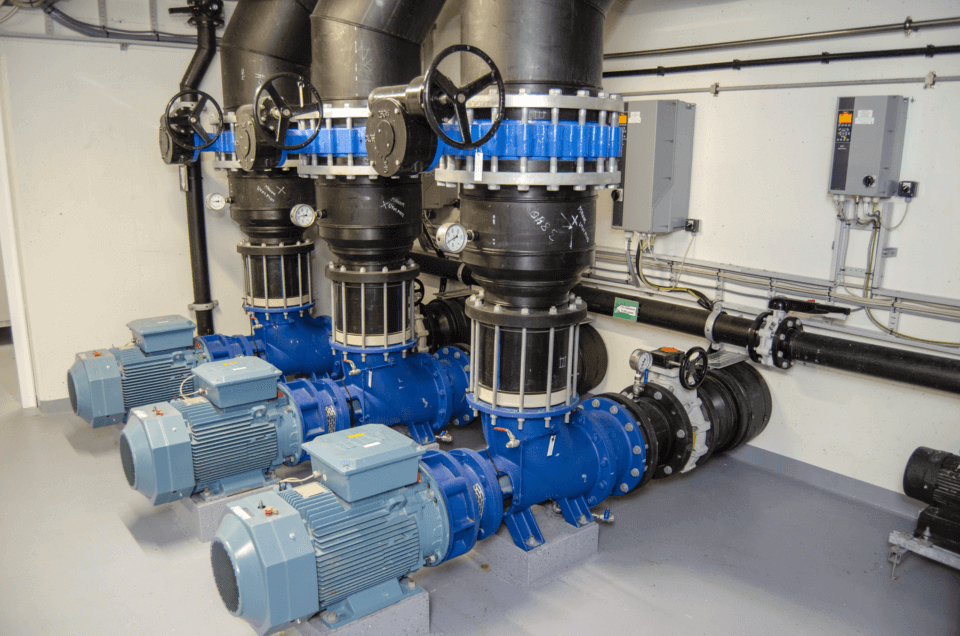
Feed factor
By switching to RAS, a better feed factor has been achieved than before.
– In actual fact, instead of filtering the water before releasing into the environment, we return the water into the farm, so the environment is present in the facility. With RAS, we need to be more on the cutting edge of water quality 24/7. It is monitored hourly and the operation must be increasingly sharp, says Mathias, who considers RAS as a sustainable and exciting way of fish farming.
An important experience is that the particle filters, which are integrated in the plant, are central and almost more important to keep an eye on than watching the fish itself. Because the filters constantly take out significant amounts of organic sludge, they are the main key to good operation. They also ensure that the biofilters are not overloaded and that the water treatment is in balance.
– The filter sludge represents a resource. Achieving a high proportion of dry matter in the sludge is important for the economy in the long run. Recently we had a visit from local contractors who want to use the sludge for biogas production, says Eidesvik.
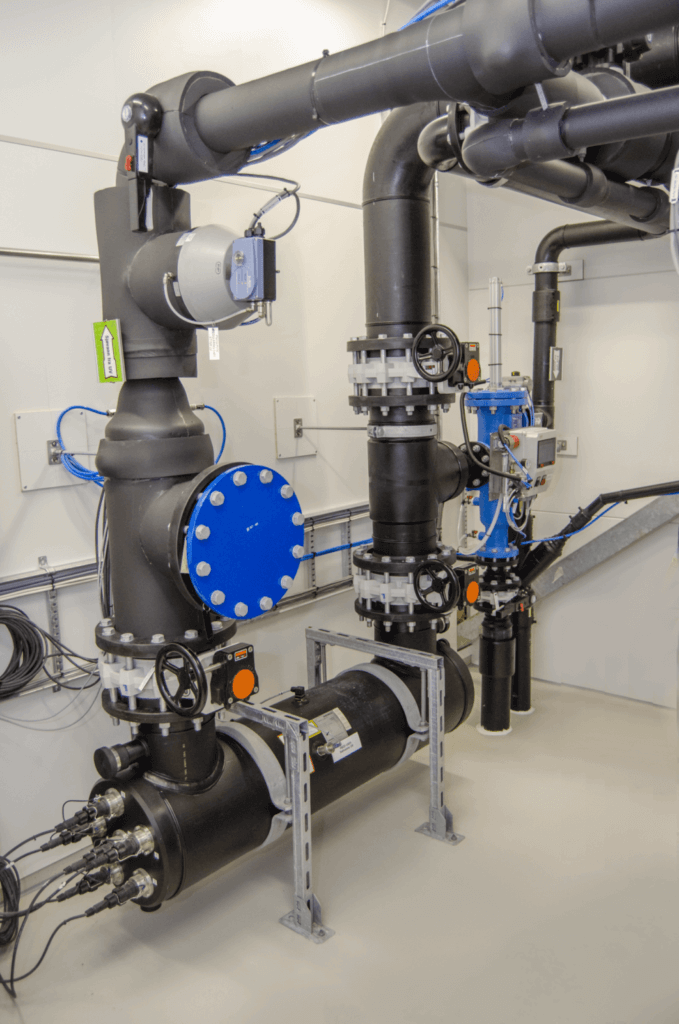
Aeration and cooling
Since the water is circulating, there is a need for temperature regulation. The intake water can be chosen at different depths(water temperature) in water source. In addition, both heat exchangers and heat pumps are ready to regulate the water temperature up or down, but this has not so far been necessary.
– The next winter, we will see if there is a need for a heat supplement. We have a low water demand, and it seems that we have an energy-efficient plant. The RAS system does not need more energy than what we used in the flow-through system, says Eidesvik.
Robust design and easy operation are two important goals achieved at the RAS facility. The facility is logical, simple and compact. Both pumps and oxygen systems have a lot of extra capacity.
– The system is easy to operate and easy to keep clean, and not least with new inserts. We now produce excellent fish that grow very well. The temperature is stable and at the desired level. We are in a phase where we gather experience and knowledge, and we greatly appreciate the follow-up we have received from Sterner, who has delivered the facility. I have the impression that a panel of experts monitor the water quality at all times. It is reassuring. We proceed cautiously and want to be good at operation. We have also seen that the sludge treatment seems properly designed.
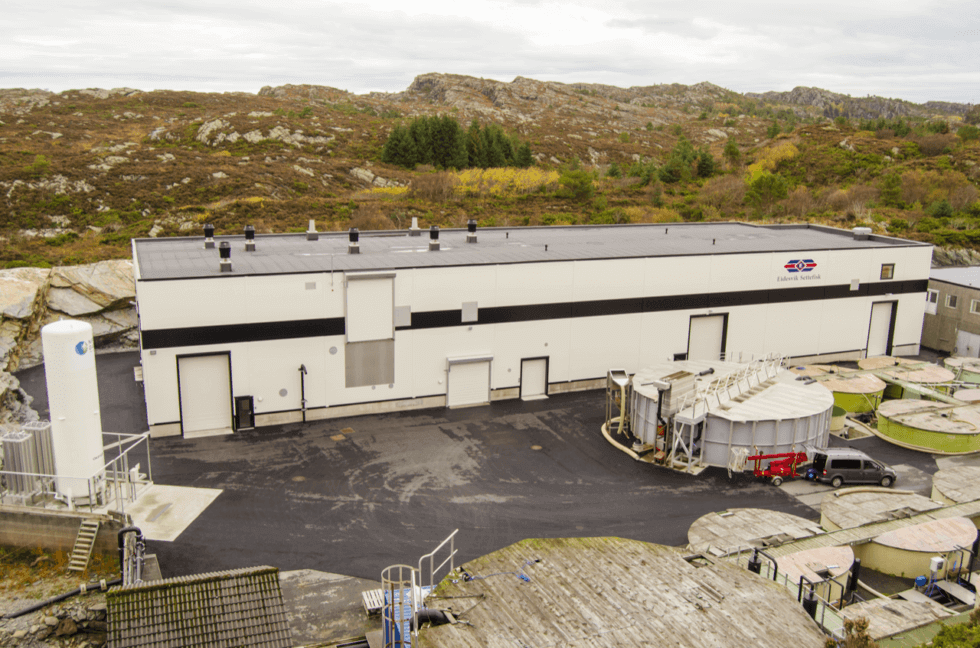
The four inserts
The fish tanks are designed with a flow pattern that provides a short residence time on fish faeces and feed residue and a high degree of self-cleaning. New water is supplied via submerged pipes, which have visual pressure indicators in the form of water jets. There are three outlets, where two side drains sit high on the fish tanks where most of the water goes out, and one drain in the middle of the bottom. Here, the rest of the wastewater brings out it feed residues and fish faeces, due to the hydraulics.
This facilitates concentrating the sludge at the vessel level. There is a separate pipe for delivering fish from the center of the tank. The plant is dimensioned to be able to feed 1500 kg per day.
– Since we have upper restrictions on cage volume in our own sea farms, we will probably also deliver smolts to others. With RAS, we have gained greater capacity and more freedom to deliver fish of the desired size as well as the time for launching, says Eidesvik.
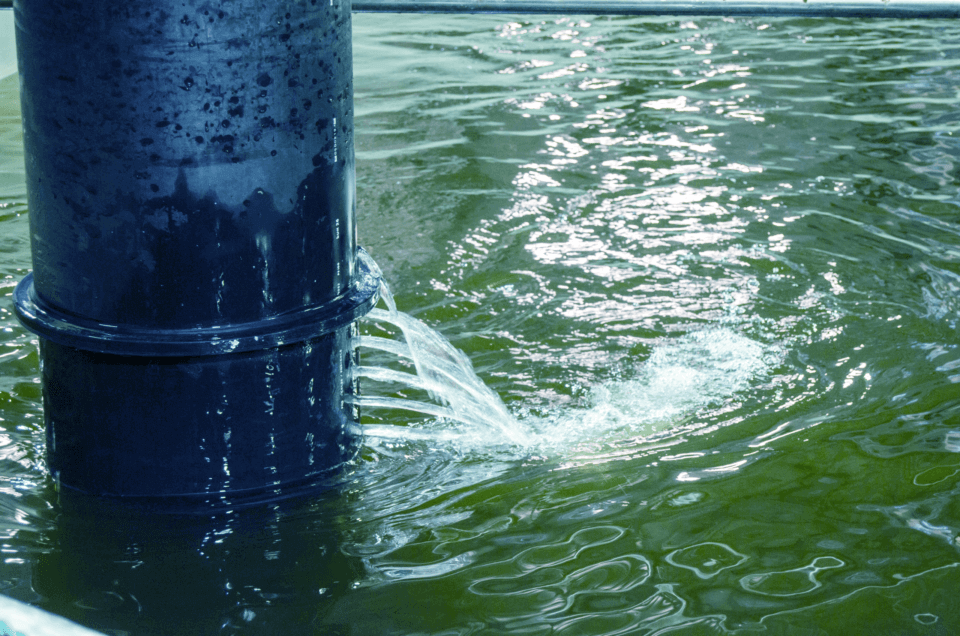
Separate department
The water treatment section is located in a separate unit and consists of a drum filter and biofilter. To keep the CO2 content low in the water, CO2 removal takes place in two stages, one before and one after the biological treatment stage. The first step is stripping off CO2 by blowing air into the water masses at a relatively shallow depth. In the second stage, a trickle filter is used in a cascade with an exhaust driven by fans.
The biological stage is a moving bed reactor system where bacteria for the decomposition of TAN * grow on plastic bodies, also called biofilm carriers. Air is added to the water to get good movement and mixing, which also ensures the removal of nitrogen. The water is continuously added oxygen, and this is dimensioned to be able to deliver double capacity if necessary.
– Our measurements indicate that the first part of CO2 aeration has not yet been necessary. We will follow as the plant goes towards full biomass load, in any case it seems that the plant is well dimensioned, says Mathias Eidesvik.
* Total ammonium compounds
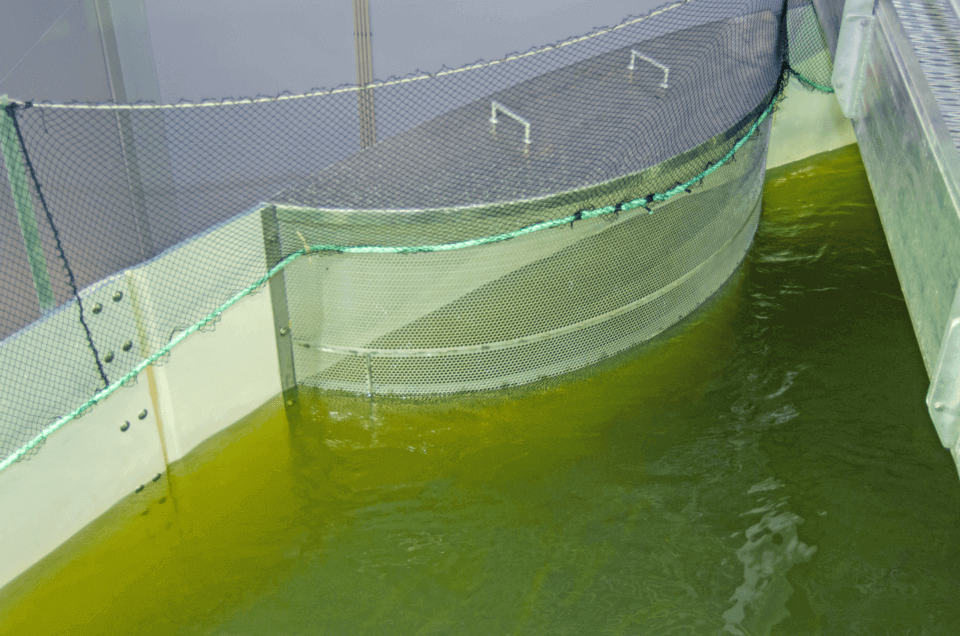